Arlene Dedier
Principal, Managing Director & Canadian Leader, Project Management Services


- Principal, Managing Director & Canadian Leader
- Project Management Services
What trends are we seeing in office tenant improvements today and what are the associated costs?
The modern office is transforming into a vibrant, activity-based destination. Employers are keen on making the office a place where employees want to be, not just need to be – more on this in our latest Viewpoints article about mastering the art of rethinking space. This shift is driven by the need to re-engage employees and make the commute worthwhile. Offices are now designed to support collaboration and learning, offering spaces that are amenity-rich and hospitality-focused. Imagine walking into an office with a welcoming front-of-house reception, not just a receptionist but a great coffee bar where you can meet clients or colleagues. Training facilities, light-filled spaces, and a residential feel are becoming standard. The concept of biophilia, incorporating plants and greenery, is gaining traction. Drop-in spaces, lockers, and flexible workstations are essential, providing employees with choices on how, where, and when they work. This evolution is about creating a dynamic environment that fosters collaboration and innovation while accommodating the flexibility of working from home.
In terms of costs, it can vary significantly based on the level of amenities and digital integration. For a basic space, you can expect to pay around $100 per square foot.
Mid-range spaces, which include more amenities and meeting rooms, typically cost around $150 per square foot. High-end spaces, such as those for professional services firms, can exceed $200 per square foot. Additionally, the cost of AV integration can vary widely. Some offices are investing heavily in seamless digital integration, where meetings can be set up without technical assistance, creating a plug-and-play environment. Furniture costs also vary, with basic setups ranging from $25 to $35 per square foot, mid-range from $35 to $50 per square foot, and high-end professional services exceeding $50 per square foot. These costs are not regionally based but depend on the amount of furniture and equipment required for the space. Smaller tenants tend to look at buildings that already offer amenities.
Average costs $/psf
Typical space
Basic:
$100
Mid-range:
$150
High end:
$200
Furniture
Basic:
$25-$35
Mid-range:
$35-$50
High end:
$50+
Source: Avsion Young Project Management

How are tariffs impacting the construction costs of these improvements?
Tariffs are exerting significant inflationary pressures on the construction industry, particularly affecting metals like steel and aluminum. The direct cost increase is compounded by a butterfly effect, where components made in the U.S. impact the cost of Canadian-made products. This ripple effect extends to logistical delays, as materials can be stuck in ports, creating bottlenecks.
Manufacturers are now stockpiling material, but there may be a queue once the stocks are depleted.
Avison Young is speaking with various industry representatives and manufacturers to understand how much of their product is made here or elsewhere, because China is also having tariffs imposed. So, we look to EU and UK manufacturers as alternatives to the U.S., which has a logistical impact. We can find Canadian companies for a lot of the products, but they're much smaller and will need to scale up. That is also part of the butterfly effect.
As for the materials with aluminum content that are currently in the ports, we must determine how to process that and to whom are the tariffs paid. This is already having an impact as materials can't get released because people logistically don't know how to apply the tariffs. Like the domino effect we saw during the pandemic, the container is stalled in the port, and that container is scheduled to be in another port in three weeks. It is disrupting the supply chain. So, we must analyze what we can do so that our clients can safely occupy their space and comply with all regulations.
This complexity of applying tariffs to materials already in transit adds to the delays. For example, a 25% increase in steel costs doesn't just affect steel beams but also all steel components in appliances and furniture.
"To mitigate these risks, we're implementing management reserves, which are undisclosed funds held between project managers and clients to account for unforeseen tariff impacts of longer carrying costs."
This approach helps de-risk projects by thoroughly analyzing potential risks and their probabilities. Engaging with local manufacturers and vendors is crucial to understand the full impact on materials and logistics.
While tariffs are indeed a current geopolitical challenge, we anticipate that global trade agreements will be resolved at some point over the next year. As a result, ideally any construction challenges may be mitigated following these global resolutions.

ICI building construction price inflation %

Source: Statistics Canada, Avison Young Market intelligence
Will the multiple labour trade negotiations in Ontario and Quebec have an impact on project costs and delivery?
What we've heard from general contractors is that people want to work. They're feeling the pressures of a potential economic downturn, and they want to keep things moving forward. So, we are cautiously optimistic around the subtrade negotiations outcome.
One thing we must pay more attention to is adopting technology to expedite delivery. Construction has been slow to adopt but integration is progressing to face its aging workforce challenges. Knowledge drain is starting to impact subtrades and the gap between the retiring boomers and the smaller cohort of Gen Zs and Millennials.
We don't have enough people joining the construction trades as we address not just the commercial industry, but the housing industry and infrastructure. That is something we are paying attention to as we're going to see it come to a head in the next five years.
Expiring collective agreements by jurisdiction, and expiry date
Quebec Construction
Expiry Date:
April 30, 2025
Jurisdiction:
Quebec
Ontario ICI Construction
Expiry Date:
April 30, 2025
Jurisdiction:
Ontario
Alberta Construction
Expiry Date:
June 30, 2025
Jurisdiction:
Alberta
B-Columbia Construction
Expiry Date:
December 31, 2025
Jurisdiction:
British Columbia
Manitoba Construction
Expiry Date:
October 31, 2025
Jurisdiction:
Manitoba
Source: Statistics Canada, Avison Young Market intelligence
Inflation in major building material
Industrial
Highest YoY increase
of cost index item:
Equipment + 5.73%
Plumbing + 5.53%
Exterior improvements + 5.30%
Highest three-year increase
of cost index item:
Metal Fabrication + 49.09%
Structural steel framing + 48.25%
Concrete + 35.61%
Office
Highest YoY increase
of cost index item:
Conveying equipment + 6.51%
Earthwork + 6.01%
Utilities + 5.85%
Highest three-year increase
of cost index item:
Metal fabrication + 48.36%
Structural steel framing + 47.11%
Equipment + 42.00%
Retail
Highest YoY increase
of cost index item:
Plumbing + 5.32%
General requirements + 5.14%
Finishes + 5.12%
Highest three-year increase
of cost index item:
Metal fabrication + 45.73%
Structural steel framing + 44.45%
Finishes + 32.71%
Source: Canada’s Building Construction Price Index (BCPI)
What advice do your have for tenants in the current context?
Tenants should proactively plan ahead to navigate the butterfly effect of tariffs on their projects.
Engaging with local manufacturers and vendors to understand the full impact on materials and logistics requires time. By exploring alternative solutions, we can better manage and mitigate challenges effectively. We have dealt with inflationary pressures and material shortages before, be it during pandemic or even in 2006, when we had drywall and copper shortages. We need to be patient as the pressure eventually releases.
It's also important to consider the holistic impact of tariffs, including logistical delays and increased carrying costs. For example, a project that would typically take six months may now take seven months due to supply chain issues. Tenants should also explore locally made alternatives and understand the percentage of Canadian-made products in their projects. This proactive approach will help tenants stay ahead in an uncertain market.

“Tenants should also explore locally-made alternatives and understand the percentage of Canadian-made products in their projects.”
Reach out to Arlene Dedier to learn more.
Arlene Dedier
-
- Principal, Managing Director & Canadian Leader, Project Management Services
-
- Project Management
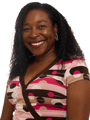